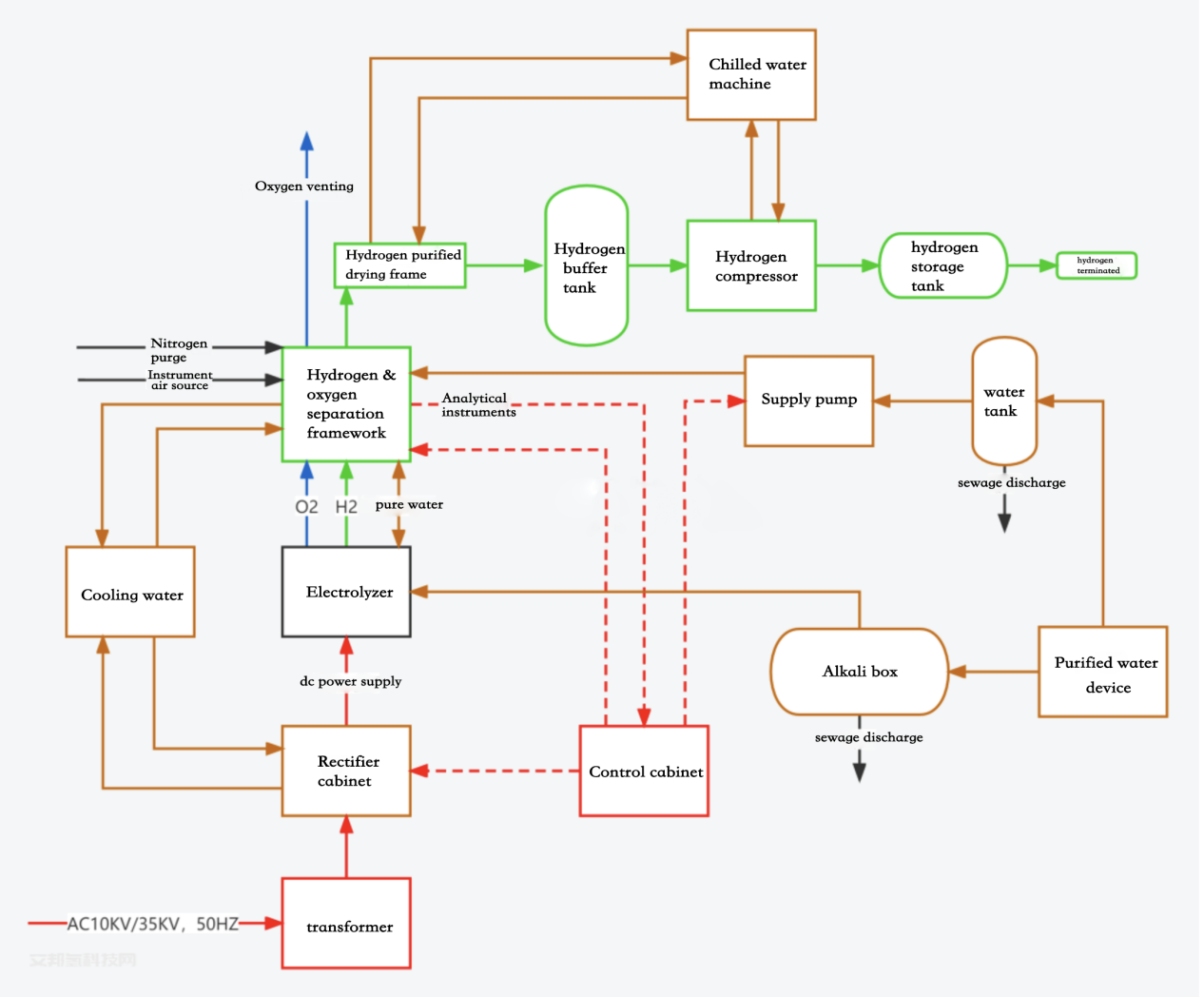
The electrolysis hydrogen production unit includes a complete set of water electrolysis hydrogen production equipment. The main equipment is:
1. Electrolyzer
2. Gas-liquid separation device
3. Drying and purification system
4. The electrical part includes: transformer, rectifier cabinet, PLC program control cabinet, instrument cabinet, power distribution cabinet, host computer, etc.
5. The auxiliary system mainly includes: alkali tank, raw material water tank, water supply pump, nitrogen bottle/bus bar, etc.
6. The overall auxiliary system of the equipment includes: pure water machine, cooling water tower, chiller, air compressor, etc.
In the electrolytic hydrogen production unit, water is decomposed into one part of hydrogen and 1/2 part of oxygen in the electrolyzer under the action of direct current. The generated hydrogen and oxygen are sent to the gas-liquid separator together with the electrolyte for separation. The hydrogen and The oxygen is cooled by the hydrogen and oxygen coolers, and the drop catcher catches and removes water, and then is sent out under the control of the control system; the electrolyte passes through the hydrogen, oxygen alkali filter, hydrogen, oxygen alkali filter, etc. under the action of the circulation pump. liquid cooler and then return to the electrolyzer to continue electrolysis.
The pressure of the system is adjusted through the pressure control system and differential pressure control system to meet the requirements of subsequent processes and storage.
Hydrogen produced by water electrolysis has the advantages of high purity and few impurities. Usually, the impurities in hydrogen produced by water electrolysis are only oxygen and water, and no other components (which can avoid poisoning of some catalysts), which provides convenience for producing high-purity hydrogen. , after purification, the gas produced can reach the indicators of electronic grade industrial gas.
The hydrogen produced by the hydrogen production device passes through a buffer tank to stabilize the working pressure of the system and further remove free water in the hydrogen.
After the hydrogen enters the hydrogen purification device, the hydrogen produced by water electrolysis is further purified, and oxygen, water and other impurities in the hydrogen are removed using the principles of catalytic reaction and molecular sieve adsorption.
The equipment can set up an automatic adjustment system for hydrogen production according to the actual situation. Changes in gas load will cause fluctuations in the pressure of the hydrogen storage tank. The pressure transmitter installed on the storage tank will output a 4-20mA signal and send it to the PLC and After comparing the original set value and performing inverse transformation and PID calculation, a 20~4mA signal is output and sent to the rectifier cabinet to adjust the size of the electrolysis current, thereby achieving the purpose of automatic adjustment of hydrogen production according to changes in hydrogen load.
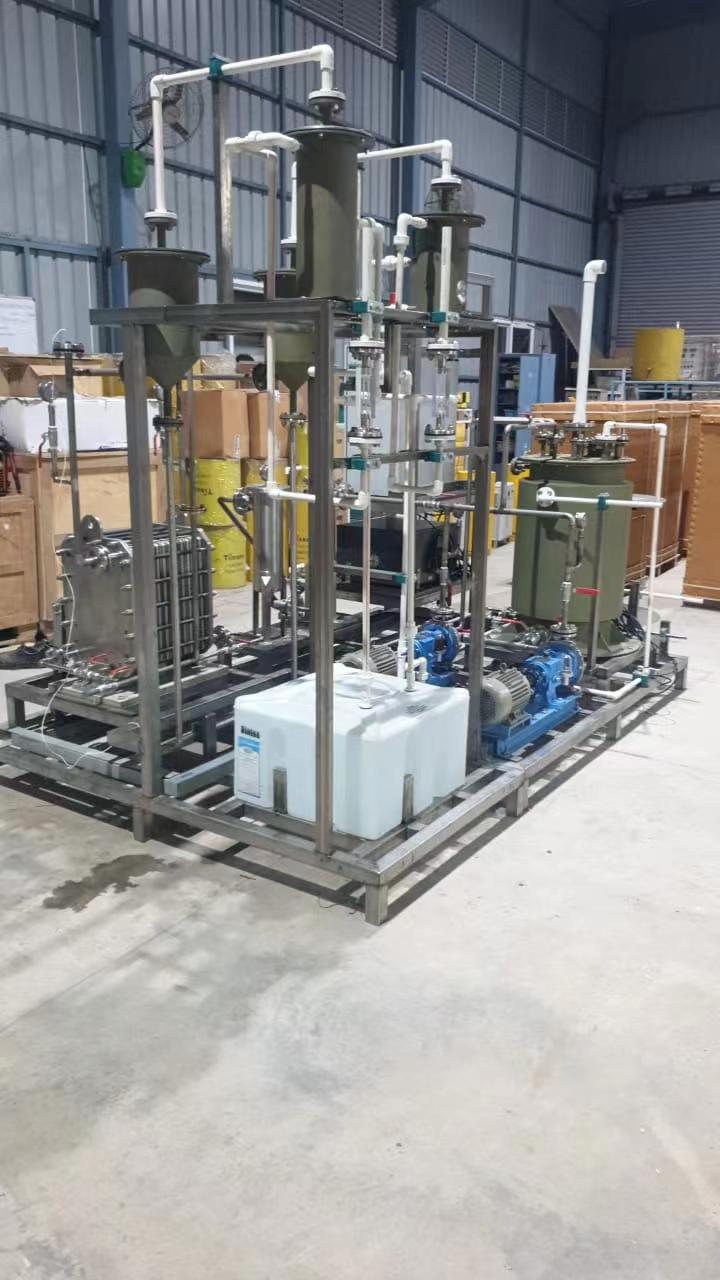
Alkaline water electrolysis hydrogen production equipment mainly includes the following systems:
(1)Raw material water system
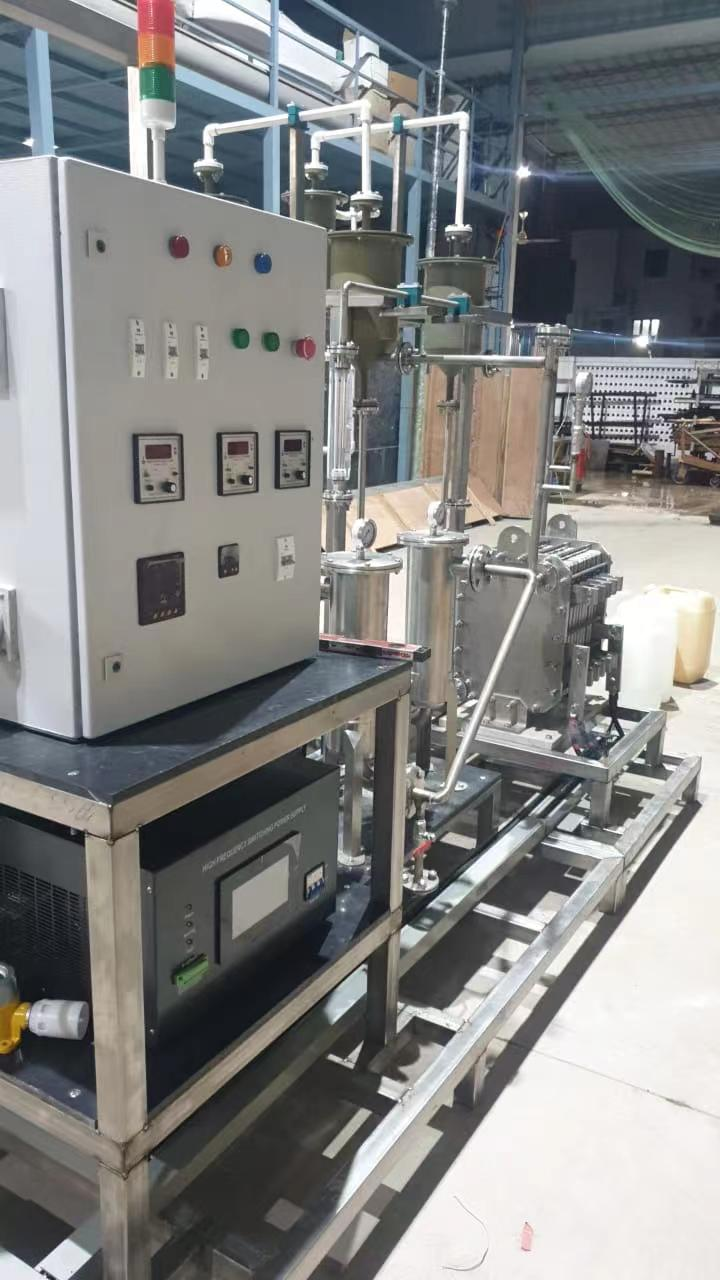
The only thing that reacts in the water electrolysis hydrogen production process is water (H2O), which needs to be continuously replenished with raw water through a water replenishment pump. The water replenishment position is on the hydrogen or oxygen separator. In addition, a small amount of hydrogen and oxygen must be taken away when leaving the system. of moisture. The water consumption of small equipment is 1L/Nm³H2, and that of large equipment can be reduced to 0.9L/Nm³H2. The system continuously replenishes raw water. Through water replenishment, the stability of the alkali liquid level and alkali concentration can be maintained, and the reaction solution can be replenished in time. of water to maintain the concentration of the lye.
2) Transformer rectifier system
This system mainly consists of two devices: a transformer and a rectifier cabinet. Its main function is to convert the 10/35KV AC power provided by the front-end owner into the DC power required by the electrolyzer, and supply DC power to the electrolyzer. Part of the supplied power is used to directly decompose water. The molecules are hydrogen and oxygen, and the other part generates heat, which is taken out by the lye cooler through cooling water.
Most of the transformers are oil-type. If placed indoors or inside a container, dry-type transformers can be used. The transformers used in electrolytic water hydrogen production equipment are special transformers and need to be matched according to the data of each electrolyzer, so they are customized equipment.
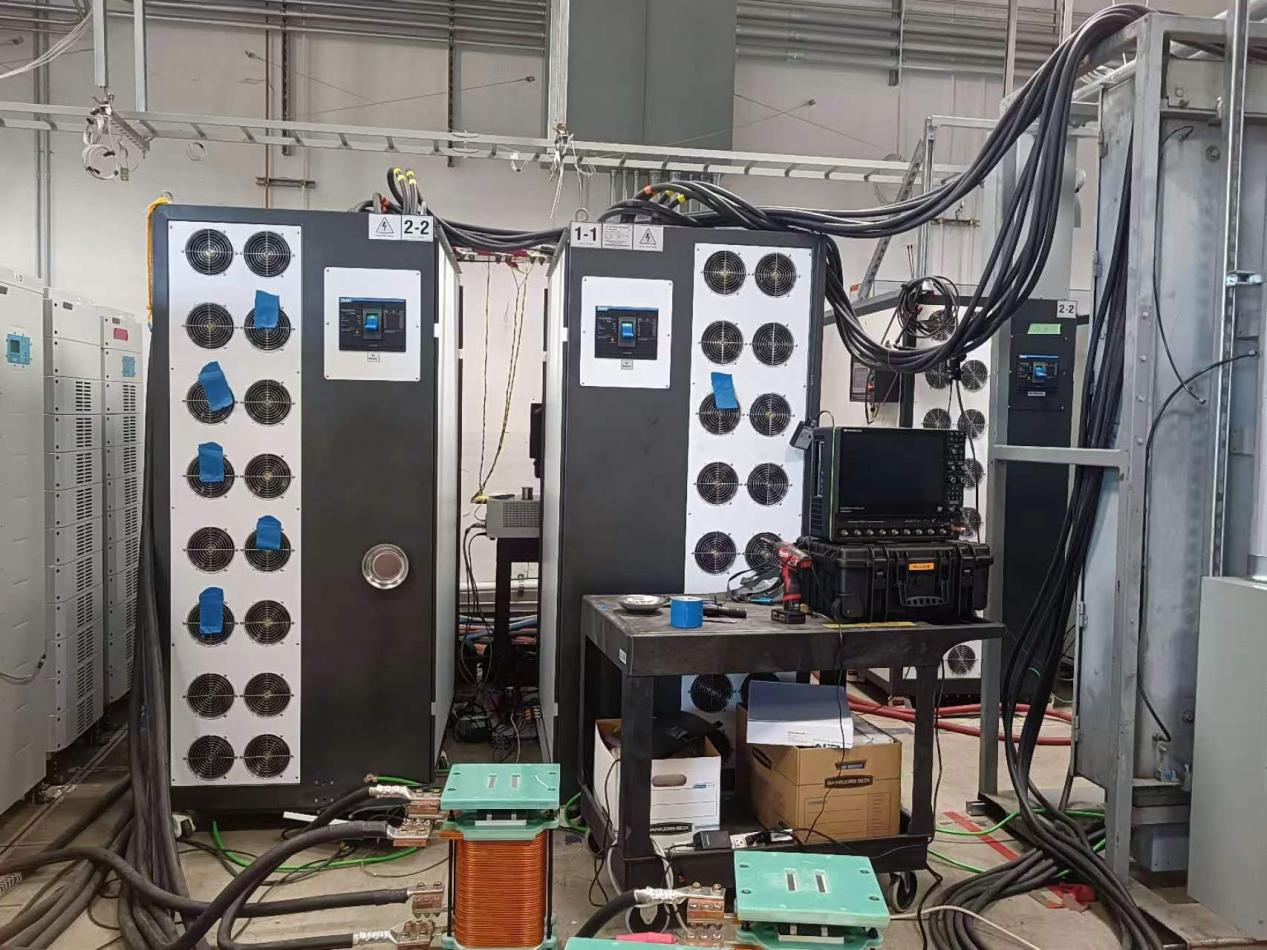
(3) power distribution cabinet system
The power distribution cabinet is mainly used to supply 400V or commonly known as 380V equipment to various components with motors in the hydrogen and oxygen separation and purification systems behind the electrolytic water hydrogen production equipment. The equipment includes the alkali circulation in the hydrogen and oxygen separation framework. Pumps, water replenishment pumps in auxiliary systems; heating wires in drying and purification systems, and auxiliary systems required by the entire system, such as pure water machines, chillers, air compressors, cooling towers, and back-end hydrogen compressors, hydrogenation machines and other equipment Power supply also includes power supply for lighting, monitoring and other systems of the entire station.
(4) control system
The control system implements PLC automatic control. The PLC generally uses Siemens 1200 or 1500. It is equipped with a human-computer interaction interface touch screen, and the operation and parameter display of each system of the equipment and the display of control logic are realized on the touch screen.
5)Alkali circulation system
This system mainly includes the following main equipment:
Hydrogen and oxygen separator - alkali circulation pump - valve - alkali filter - electrolyzer
The main process is: the alkali liquid mixed with hydrogen and oxygen in the hydrogen and oxygen separator is separated by the gas-liquid separator and then flows back to the alkali liquid circulation pump. Here the hydrogen separator and the oxygen separator are connected, and the alkali liquid circulation pump will reflux. The alkali liquid circulates to the valve and alkali liquid filter at the rear end. After the filter filters out large impurities, the alkali liquid circulates to the inside of the electrolyzer.
(6)Hydrogen system
Hydrogen is generated from the cathode electrode side and reaches the separator along with the alkali liquid circulation system. In the separator, because the hydrogen itself is relatively light, it will naturally separate from the alkali liquid and reach the upper part of the separator, and then pass through the pipeline for further separation and cooling. After water cooling, the drop catcher catches the drops and reaches a purity of about 99%, which reaches the back-end drying and purification system.
Evacuation: The evacuation of hydrogen is mainly used for evacuation during startup and shutdown, abnormal operation or purity failure, and fault evacuation.
(7) Oxygen system
The path for oxygen is similar to that for hydrogen, but in a different separator.
Evacuation: At present, most of the oxygen projects are treated by evacuation.
Utilization: The utilization value of oxygen is only meaningful in special projects, such as some application scenarios that can use both hydrogen and high-purity oxygen, such as optical fiber manufacturers. There are also some large projects that have reserved space for the utilization of oxygen. The back-end application scenarios are the production of liquid oxygen after drying and purification, or the use of medical oxygen through a dispersion system. However, the refinement of these utilization scenarios has yet to be determined. Further confirmation.
(8)cooling water system
The electrolysis process of water is an endothermic reaction. The hydrogen production process must be supplied with electric energy. However, the electric energy consumed by the water electrolysis process exceeds the theoretical heat absorption of the water electrolysis reaction. That is to say, part of the electricity used by the electrolyzer is converted into heat. This part The heat is mainly used to heat the alkali circulation system at the beginning, so that the temperature of the alkali solution rises to the 90±5°C temperature range required by the equipment. If the electrolyzer continues to work after reaching the rated temperature, the heat generated needs to be used Cooling water is brought out to maintain the normal temperature of the electrolysis reaction zone. The high temperature in the electrolysis reaction zone can reduce energy consumption, but if the temperature is too high, the membrane of the electrolysis chamber will be destroyed, which will also be detrimental to the long-term operation of the equipment.
This device requires the operating temperature to be maintained at no more than 95°C. In addition, the generated hydrogen and oxygen must also be cooled and dehumidified, and the water-cooled silicon controlled rectifier device is also equipped with necessary cooling pipelines.
The pump body of large equipment also requires the participation of cooling water.
(9) Nitrogen filling and nitrogen purging system
Before debugging and operating the device, the system must be filled with nitrogen for air tightness testing. Before normal startup, the gas phase of the system is also required to be purged with nitrogen to ensure that the gas in the gas phase space on both sides of the hydrogen and oxygen is away from the flammable and explosive range.
After the equipment is shut down, the control system will automatically maintain pressure and retain a certain amount of hydrogen and oxygen inside the system. If the pressure is still found when the equipment is turned on, there is no need to perform purging. However, if all the pressure is removed, it will need to be purged again. Nitrogen purge action.
(10) Hydrogen drying (purification) system (optional)
The hydrogen produced from water electrolysis is dehumidified by a parallel dryer, and finally dusted by a sintered nickel tube filter to obtain dry hydrogen. (According to the user's requirements for product hydrogen, the system may add a purification device, and the purification uses palladium-platinum bimetallic catalytic deoxidation).
The hydrogen produced by the water electrolysis hydrogen production device is sent to the hydrogen purification device through the buffer tank.
The hydrogen first passes through the deoxygenation tower. Under the action of the catalyst, the oxygen in the hydrogen reacts with the hydrogen to generate water.
Reaction formula: 2H2+O2 2H2O.
Then, the hydrogen passes through the hydrogen condenser (which cools the gas to condense the water vapor in the gas to generate water, and the condensed water is automatically discharged out of the system through the liquid collector) and enters the adsorption tower.
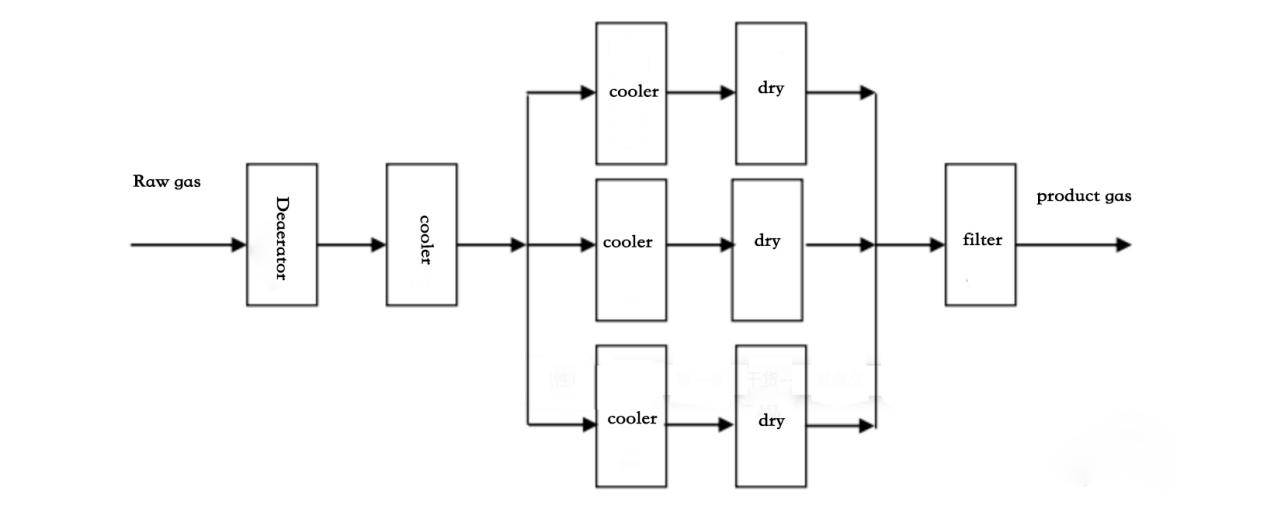
Post time: May-14-2024